
Assembly lines are everywhere in mass production. From mobile phones to cars to airplanes, almost all items produced in large quantities come from an assembly line. Just look around you wherever you are and try to find a produced item that did NOT come from an assembly line. My general recommendation is that if you can make it on an assembly line, then you probably should make it on an assembly line.
However, assembly lines are not always loved by the workers. Every few years, another—usually European—car maker is in the news about undoing the assembly line in favor of group work, box assembly, assembly stations, and the like. So far, all of these initiatives have dwindled and died, simply because the assembly line is the best! Let’s have a look at the long list of car companies that tried and failed with undoing the assembly line. The assembly line is still king in manufacturing!
Before There Were Assembly Lines

Before the introduction of the assembly line, automobiles were produced using the coach-building method. This process involved skilled craftsmen who would build each car by hand, one at a time. The process was slow, labor-intensive, and expensive, making cars a luxury item only available to the wealthy.
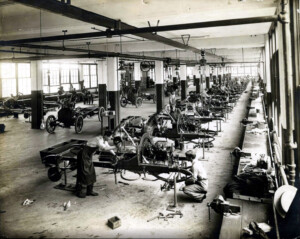
The production was in so-called assembly rooms, where a car was built on one spot. All material, tools, and the workers converged on this spot to assemble a car. This was easiest to set up, as management did not have to coordinate work between different stations. However, it was much more difficult to actually run these systems on the shop floor. Missing material, delayed material, and material delivered too early were constant problems. The coordination between different workers was also often lacking, and it was hard to keep track what had already been done and what was still to be done. Especially if workers came to the station to do only one specific set of tasks, it was quite possible that they overtook each other, and that the next worker had to undo previous work since it prohibited him from doing his own work. Imagine installing the doors before adding the seats or the dashboard. Now it will be much more difficult to get the seats or the dashboard into the car since the doors are in the way.
The Assembly Line

The concept of the assembly line evolved over time. Some consider the Arsenal of Venice an assembly line. Assembly lines were definitely in use for baking biscuits for the British navy in Plymouth in 1833. Chicago slaughterhouses established “disassembly” lines around 1837 to take apart pigs. James Bonsack invented the cigarette rolling machine in 1881, which eventually turned into a full-blown assembly line. Around the same time, assembly lines for matches and tin cans appeared.

In automotive, Oldsmobile is often claimed to be the first assembly line, but due to the lack of interchangeable parts, I would consider the first automotive assembly line to be Henry Ford’s in 1913. Nowadays, assembly lines are the standard for mass production due to their efficiency, speed, ability to be planned, and low cost. All these easily outweigh the additional effort to set up and organize an assembly line.
Criticism of Assembly Lines
Assembly lines have often been criticized for dehumanizing work. The repetitive nature of the tasks, the strict time constraints, and the lack of autonomy can lead to a loss of individuality and a sense of disconnection from the final product. Workers may feel like mere cogs in a machine rather than valued contributors to the production process.
This criticism is particularly prevalent in Europe, especially in Germany, where the workplace is often seen as a social institution. In contrast, in the United States, the hire-and-fire mentality is much more widespread, leading to a different perception of the role of the worker in the production process.
Volkswagen Salzgitter 1975
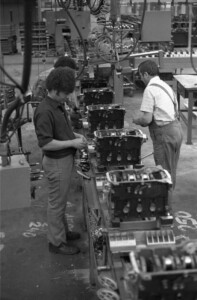
In 1975, Volkswagen Salzgitter conducted an experiment of group assembly of engines by twenty-eight workers in four teams. These teams were also responsible for material transport, testing, and repair, and the groups were assigned tasks internally. While a normal engine assembly had a cycle time of one minute, the station had forty-five minutes of work content.
However, the experiment was not successful. Workers’ representative groups felt threatened as the worker groups negotiated with management directly. No hard performance data was available, but management considered this method not suited for mass production. The experiment was closed in 1977 after two years.
Volvo Kalmar 1984
In 1984, Volvo conducted an experiment in Kalmar, Sweden, where they eliminated assembly lines. Instead of the car moving down the assembly line, it was assembled in one spot by a group of about ten workers. In effect, this was a reversal of car manufacturing to before Henry Ford’s assembly line. This method was called Volvoism and was implemented due to problems in recruiting new workers and higher turnover. Out of all the experiments shown here, this is probably the best-known one.
However, the experiment was not successful. While worker satisfaction was somewhat higher than in conventional assembly lines, productivity was not. The demand for materials and parts clashed with standard material transport, and quality did not improve. Even the stress levels of workers remained about the same. Eventually, in 1987, Volvo decided to change Kalmar back to a conventional assembly line. The experiment lasted three years. The plant closed in 2013.
Opel Bochum around 1988
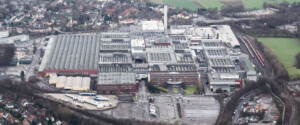
In 1988, Opel Bochum (start of production 1963) conducted group assembly experiments. These experiments involved cockpit assembly in groups, with a work cycle of fifteen to forty-five minutes. An AGV carried the cockpit to the next station. A publication from 1991 claimed that a wide rollout of this method was planned for the entire company. However, not much information is available on this topic, and it is not known if the rollout ever took place. Personally, I don’t believe that, and I think they are using assembly lines just like everybody else. In any case, the plant closed in 2014.
As it turns out, the list of car plants that experimented with undoing the assembly line is so long that I need another blog post. Three more (unsuccessful) experiments will be shown in my next post. Now, go out, do NOT undo your assembly line, and organize your industry!
Interesting post Christopher.
I have also experienced a strong reluctance from workers to move from a ‘coach-building’ set up to becoming part of an assembly line. While the sense of job satisfaction is greater, the internal logistics becomes duplicated at each work area.
In addition, the learning curve required for an Operator to build a product with 30-40 minutes of work content, from start to finish, is very steep, compared to learning a 4 minutes cycle, typical of one of our assembly-line stations.