When we are talking about lean manufacturing, we often focus on the tools like kanban, 5S, SMED, and many more. Sometimes, but harder to grasp, is the underlying culture and philosophy of continuous improvement and PDCA. Part of this culture is what you could call the soft power of the Toyota Production System. This is a form of decision making in contrast with the “hard power” more common in Western companies. Let’s have a look:
Hard Power
Hard power is decision-making power established through hierarchy. In the end, the boss makes the decision and the employees have to accept it, no matter whether they want it or not. This is also the formal and legal approach, as the boss has the authority to make decisions even if the underlings disagree. The advantage of this approach is its speed. It is faster for one person to make up his mind and form a decision, than for ten people to do so.
Flaws of Hard Power
However, such hard power also has its disadvantages. For one thing, the wisdom and experience of a group usually exceeds the wisdom and experience of a single person, no matter how much more money he makes and how much bigger his desk is. Hence, a group agreeing on a decision usually makes better decisions than an individual on his own.
But a second disadvantage of a unilateral decision by the boss is that the employees may not agree. Now, in purely legal terms, the employees have to suck it up and just deal with it, as they are legally obliged to follow the orders of their boss. But only a fool would believe this to be absolutely true. Even though it is not part of the legal system (usually written by the bosses), employees have a multitude of ways to disagree and obstruct any decision by their management. From dragging their feet to strictly following instructions (probably the worst) to complaining behind their boss’s back (probably the most common) to many other forms of obstruction due to a lack of commitment and a loss of morale.
Soft Power in Japan
In Japan and at Toyota, there are often (but not always) some softer approaches to decision making. Instead of forcing a decision on the employees and subordinates, more effort is put into bringing them on board. This is in part due to the Japanese tendency to risk aversion, wanting to make sure there are no surprises or opposition when proposing a new decision. Below I have a couple of Japanese terms related to these softer approaches.
Nemawashi
Nemawashi (根回し) is Japanese for “laying the groundwork; behind-the-scenes maneuvering; consensus-building process.” This is an informal process of talking to people, warming them up to your idea, and listening to them to get their feedback and hear their concerns. The goal is to get their consensus before formally proposing a change. Hopefully the final agreement is then a mere formality, because all (or most?) sides have already agreed beforehand. This also makes it easier to work with disagreement. If another person rejects the idea formally in front of everybody, it is much harder and potentially includes much more loss of face for them to change their opinion. An informal rejection during small talk, on the other hand, can be much easier overcome through consensus finding.
On a side note, nemawashi comes from ne (根) for roots of a plant and mawasu (回す) for turning or rotating, and is also a gardening term for carefully digging around the roots of a tree or other plant before transplanting, rather than ripping out the plant. Similarly, in a company you talk your way around before proposing the decision. Different from lobbying, nemawashi is more of a consensus building and transparent communication approach.
Yokoten
Yokoten is actually an abbreviation common at Toyota for yokotenkai (横展開) for horizontal deployment or application to other fields. The idea is to share leanings and experience across the entire company. You could call it a best-practice sharing across an organization. These best practices can be technical, organizational, or other, not only on the outcomes but also on the process. It is sometimes also written as Yokoni Tenkai (横に展開), but carries the same meaning.
Hansei
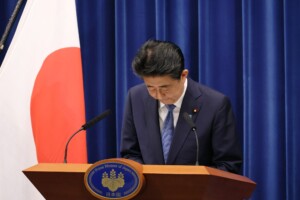
Hansei (反省) means reflection; reconsideration; introspection; meditation; or contemplation. This is a sequence of self-reflection, taking responsibility, and committing to improvement. This is generally a part of Japanese culture and aims to both understand and admit your own mistakes and flaws. While in the Western world, admitting guilt often opens you up for even more attacks, in Japan it is seen as a step toward improvement. And, yes, it can involve a lot of bowing.
Hourensou
Hourensou (報連相) is also an abbreviation for houkoku (ほうこく or 報告) for report or inform; renraku (れんらく or 連絡) for contacting or messaging; and soudan (そうだん or 相談) for consultation or discussion. This is a mnemonic in Japan for a style of reporting. The same pronunciation is also the word for Spinach, but written as ほうれん草.
The first word stand for a report by a subordinate or colleague that should include all relevant information. Next, all stakeholders are informed about the current status. The third word refers to discussing with others on the next steps, decisions, and actions. The idea is to do it frequently. The method does not originate from Toyota but from a financial firm around 1982. The opinion on this is divided. Some believe the frequent communication will improve business processes; others believe that this has a too high demand for the work time of both employees and managers.
Tatakidai
Tatakidai (叩き台 or たたき台) is a springboard for discussion; draft proposal; or tentative plan. It also means chopping board. The idea is to seek consensus and informing others when the project is 80% complete to improve chances of acceptance. In English, “to put your head on the chopping block” has a completely different meaning of taking a risk and putting yourself in harm’s way. In Japan, it is the total opposite and Tatakidai is used to avoid risks and for slow consensus building. You discuss the proposal with colleagues while it is not yet completed, giving them a chance to update or modify the proposal before it is officially presented for a decision.
Advantages and Disadvantages of Soft Power
Of course, such a soft-power approach is not perfect either. Decisions usually take longer since you have to include everybody and do a lot of talking. On the plus side, once the decision is made, it is much less likely that people are still against it and will try to torpedo the decision. Besides, there are also plenty of managers in Japan and even in Toyota who are not that good at these soft-power approaches to decision making. The former CEO of Toyota, Akio Toyoda, is one such example where his decision counts and is not to be questioned.
In any case, you have to find a balance between making a decision yourself and a decision where all stakeholders were involved beforehand. The latter is often easier afterward. Now, go out, involve your people in your decision, and organize your industry!
This is an excellent article which has increased my vocabulary of Toyota expressions, thank you.
However, it saddens me that an article like this has to be published almost half a century after Lean was discovered. It suggests that the Lean movement does not practice hansei.
Some of the reasons you might want to explore:
1. The Lean education model is a busted flush: expecting leaders and managers to coach their people when they have no experience coaching and firmly believe in Command & Control makes no sense;
2. Lean is far too lucrative a revenue stream for so-called Lean experts for it to be allowed to enter the educational mainstream. By now, can’t this be taught to high-school students; to apprentices and to undergraduates?
3. The Teflon coating that has resisted Lean Thinking is the result of the Friedmanites who infest organisations and who focus on maximising shareholder value despite what this does to the health of an organisation because increasing profit also benefits them;
4. The B-Schools across the world reject Lean Thinking because this is an anathema to the Friedmanism they teach their MBA students.