As part of my grand tour of German automotive, I visited the BMW plant in Leipzig. As of now, this is my second most favorite German automotive plant, after BMW in Munich. I will talk more about this quite well-organized and indeed beautiful plant in a later post series, but in this post I’m going to explain their very interesting and novel way to set up their assembly line. They call this the finger structure or comb structure (Fingerstruktur or Kammstruktur) because the line layout looks like the fingers of a hand or the teeth of a comb. I found this approach quite unique, and hence would like to share it with you.
Introduction
The BMW plant in Leipzig is the latest plant of the BMW group (albeit another one in Hungary is under construction). Compared to their other plants in Munich and Berlin (motor bikes), Leipzig is a greenfield plant. When it started production in 2005, there was lots of space and not much around it (compared to Munich and Berlin being in the middle of the city). Hence, they could design the plant and its material flow with little restrictions.
The central point for the material flow is the main office, which is a quite fancy design by famous Iraqi-British architect Zaha Hadid. She is known for her flowing forms, and there are almost no right angles in the central building, with open offices. All cars flow through the central building multiple times, and are displayed very prominently. I quite like the design.
The material flows from the press shop and the body shop (in the upper left in the aerial photo) to the paint shop (in the lower middle), and from there to the assembly building on the right. The central building is the odd-angled building between the body shop and the paint shop. If you look more closely at the assembly building, you may notice a strange shape. It is not rectangular. Instead, there are some fingers sticking out of the building.
The Fingers of the BMW Leipzig Assembly Building
We can see the fingers even more clearly on the layout. The aerial photo above is from 2005, and since then the plant has expanded a bit and more buildings have been added. In the layout below, you can see clearly the five fingers sticking out of of the assembly building. This is the defining feature of the BMW Finger type assembly line!
The assembly line runs inside the assembly building, having a loop for each finger. In the map above I just named the fingers according to the hand, albeit I am not sure if BMW does this too, or simply numbers them. In any case, the BMW plant in Leipzig happens to have five fingers, but a finger line with more or less fingers is also easily imaginable. The image here is roughly the path of the line when I visited the plant in March 2024.
This finger line gives two advantages over conventional lines. The first one is flexibility, and the second one is ease of access for material supply. BMW tried this system out for the first time in Leipzig, and found it very suitable for their purpose. They plan to use this system also for future plants (where they have the space—i.e., not Munich). To my knowledge, their plant in South Carolina is also adopting this structure. Let me go into more detail on both advantages.
Flexibility
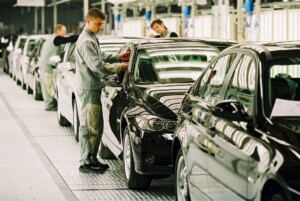
The first advantage is flexibility, and future-proofing of the line for future models. BMW usually runs all of their products on a single assembly line with a fast takt time. In Leipzig the takt is 58 seconds, which is on the faster side for automotive assembly lines. Yet, future models may have different requirements.
Most famously, when the plant started producing in 2005, electric cars were still mere concept cars for development. The first commercially available BMW electric car was the i3 in 2013, followed by the first plug-in hybrid i8 in 2014. The i3 was produced in Leipzig from the start. However, due to the different power train, the assembly line needed more space for additional stations to include the installation of batteries, cables, and other things that a combustion engine does not need.
Even if they have the same drivetrain, cars may have different features and assembly requirements, which would benefit from more (or fewer) stations on the line. Leipzig is currently producing four models, the 1 Series, the 2 Series Grand Coupe, the 2 Series Active Tourer (including hybrid), and the Mini Countryman, a completely different brand of BMW requiring even more different assembly.

Throughout the history of the plant, Leipzig produced a dozen different models that are no longer made, and numerous changes had to be made to the assembly line. Many of those needed more space on the line for new or different assembly stations. If you have already packed your existing line tightly into the available space, you are out of luck. Maybe you can extend the line at the end or the beginning.
While simply extending the line at the end or at the beginning will give you more space, chances are that you need space somewhere in the middle. To get space in the middle you would need to move all other stations down (or up) the line. And that’s where it gets expensive.
Many stations can be moved easily. You roll your material supply carts to wherever you need them, place your employees there, and organize delivery to the new location. Other stations, however, cannot be easily moved. Anything with robots makes it much more expensive to move. The merging of the engine and drivetrain with the car body also requires heavy lifting equipment, as do many other heavier items like seats, dashboards, windows, doors, and more. If your door comes from an overhead logistic system, moving the door assembly station will be a major pain.

This does not include the different transport systems for cars. Often, a car is on a moving platform. But for underbody assembly, it is often hanging or on a rotating hanger. It may be on an AGV, and at the end the car hopefully moves on its wheels under its own power. It would also be a major pain if you want to install the exhaust system under the car, and the car is on a moving platform. (Side note: Toyota tries to address the very same issue slightly differently with their new type of flexible assembly line.)
In sum, chances are that you may need space somewhere in the middle if you don’t want to move around a whole lot of expensive equipment. And that is where the fingers come in. These fingers give you space to extend your line in the middle at five different spots. You can extend the lines up to 200 meters (and back again) at five different locations until you reach the next adjacent building. This gives you a lot of flexibility. And BMW has done that. If you compare the aerial photo at the beginning of this post from 2005 with the map from 2024, you will see that quite a few fingers have grown. In 2005, there was no thumb and the index finger was shorter. The pinky also seems to have grown. These extensions can also be built while the line is running, and only connecting them requires a stop of the line.
Material Supply
A second advantage is the ease of access for material supply. The fingers are designed so that trucks can drive into the gaps and deliver material almost directly to the line. In Leipzig, 80% of the parts are delivered just in time (JIT) and just in sequence (JIS). The logistic warehouses are also built directly around the assembly building, often with bridges directly into the assembly hall. Overall, this finger design makes it much easier to get material to the point of use.
Overall, I like their line layout approach quite a lot, and think it is a smart idea. I am a bit skeptical about their concept of not stopping the line ever, even when there are problems… but that is for a later post on my grand tour of German automotive. But this layout combined with BMW’s VERY efficient production makes this plant my second favorite in Germany, after the main BMW plant in Munich. One small downside if you want to copy it, this finger structure may be patented, albeit I could not find the patent. Now, go out, make your assembly line flexible for future expansions and easy material supply, and organize your industry!