This is the third post in my series on how Fendt handles its rather large variability. As mentioned before, all of their tractors—eleven different models with countless variants—come from the same assembly line in Marktoberdorf. This includes small tractors that are just barely one meter wide and huge ones as you see here on the left. Imagine assembling motor bikes, cars, and trucks on the same assembly line, and you are getting close to the variability that Fendt has to deal with. Overall, this makes Fendt in my view one of the leading plants in the world in handling variability.
Pre-Assembly
Another way to handle variance at Fendt is pushing variance off to pre-assembly stations or lines. The main assembly at Fendt has around sixty stations. Any fluctuation can affect the entire line. Pre-assemblies are shorter, and fluctuations are easier to manager. A small buffer inventory can decouple these pre-assemblies from the main line. Two large pre-assemblies were, for example, the front axle and the rear axle, although they still produced in sequence for the main line. Around 25% of all employees on the shop floor work in a pre-assembly station.
Customizing Cells
Yet another way Fendt handles its variability is customizing cells (they call it a M1 Martrix). A tractor can get into a cell, and workers will customize the tractor to the needs of the customer. Effectively, it is a mini project shop as part of the flow shop assembly line. Depending on the model, the tractor can spend between twenty minutes and two hours in the cell, depending on the work content. A difference in work content from twenty minutes to two hours would be hard to handle within a flow line. Around 4–8% of the employees on the shop floor work in such customizing cells.
Assembly Line Side Loops
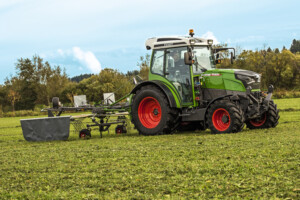
These are the main ways Fendt handles its enormous variability currently. However, the next challenge is already around the corner: e-tractors that are no longer powered by a combustion engine but by a battery. Besides them being better for the environment, it is also much easier to provide power to auxiliary tools and trailers. On the other hand, a battery lasts currently for around four to six hours, whereas a full tank of diesel lasts for around twelve. This may be an issue when you need your gear a lot during harvest period. These are scheduled to become available from Fendt this year.
Anyway, in terms of complexity this is again a major challenge. The current assembly line does not have the equipment for installing high-voltage (400V) batteries and motors. Hence, they will install a loop that branches off from the main assembly line after the cabin is installed. This loop is only for electric tractors. After the electric components are added, the tractors join the main assembly line again. This literally branches off some of the complexity.
However, since these e-tractors need more time in the separate track, the sequence will no longer be the same as before. This can potentially cause headaches again to balance all the takts and times later on. Furthermore, since the assembly time has fluctuations, it is hard to predict where in the sequence the e-tractor joins the main line again, which will challenge the handling of the variability downstream even more.
Handling Variation Summary
Overall, Fendt uses quite a few smart ideas on how to handle its rather enormous variation.
- Variable distance
- Mixed model sequencing
- Working ahead
- Separate line balancing
- Special task workers
- Pre-assembly
- Customizing cells
- Assembly line side loops
All of these help Fendt to keep its line running smoothly despite its enormous variations. As I always like to do, I estimated the percentage of value-adding time of the employees on the line, which ranged from 30% (before paint) to 43% (after paint). While this is of course not as good as an automotive assembly line at Toyota, I have seen automotive assembly lines elsewhere that were worse. Considering the enormous variation, I’d say that is a quite good use of the time of the workers. In my view, Fendt in Marktoberdorf is one of the leading plants in the world in handling variability. (Another company, Canyon Bicycles, also uses this method, but I have not [yet] seen their production line.)
But, a word of warning: This is by no means easy. A LOT of planning and organizing goes into the design of the line, the setup of the sequence, and the assignment and training of the workers. My feeling is that if you do this only sloppily, your problems will only get worse. Even at Fendt, it does not always work out as planned. The sequence is initially decided six weeks ahead of production, but, things like missing parts that sometimes happen in any factory can lead to changes to the sequence to avoid line stops. Some issues are also fixed at the end of the line in repair stations rather than stopping the line.
Currently the distance between the AGV varies, but for each AGV it is set only once at the beginning of the line. I was also wondering if there may be a use to adjust the distance between the AGV within the assembly line. While you cannot get more parts out of the line, you can adjust the available time at the stations by reducing the time for one tractor and increasing the time for another tractor. But this will make it even more complex.
Other Observations
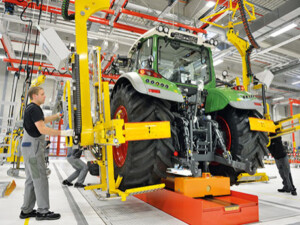
To keep problems managed, they also use an andon system. Employees at every station have two buttons to call for help in case of problems. The red button will stop the line immediately, and both the team leader and the next level supervisor (in German Meister) will be alerted via SMS. Another blue button keeps the line running until the end of the takt at this station, and only the team leader gets an SMS… for now.
With one team leader for eight to fifteen employees, support is not quite as close as with Toyota (four to five people per team leader), but much better than some other plants I have seen (twenty-five people per team leader). I also observed their shop floor meeting, and liked it. The first question by the top manager was “Were there any accidents?” After that they go through the departments one by one to give a brief summary. The whole meeting took around thirty minutes, and due to the noise levels, microphones and speakers were used. They are also a fan of KATA, which they use for problem-solving.
This concludes this three-post series on Fendt and its handling of variability. If you have additional ideas, let me know in the comments. Now, go out, master your variance, and organize your industry!
Source
The primary book on variable takt is Bebersdorf, Peter, and Arnd Huchzermeier. Variable Takt Principle: Mastering Variance with Limitless Product Individualization. ISBN 978-3-030-87169-7, Springer, 2022. (also available in German) Many thanks to Mr. Bebersdorf for explaining me his approach.
PS: Thanks to Jonathan Folberth for showing me Fendt, and to Peter Bebersdorf for explaining variable takt!
Martin Hofmann 😎
Fendt’s approach to handling variability through methods like pre-assembly and customizing cells truly exemplifies Lean Manufacturing principles in action! 🌟
Their innovative strategies not only streamline the assembly process but also maximize efficiency despite the complexity.
#LeanManufacturing
#ProcessImprovement
I’m just wondering if it shouldn’t be better to customize the e-tractor after the end of assembly. As all tractors moved on the assembly line with an AGV, it shouldn’t be a problem to move them until the end. Then they can tow the tractor to a Electric final Assembly for electrical adjustment. Maybe it is not the perfect solution but, at least, they won’t lose the sequence that is, from my point of view, very difficult to manage.
By the way, thank you for the articles about Fendt.
Hi Serge, this is also possible. The problem may be if you have to uninstall something else to get to the battery. E.g. do you need to remove the tires again to work on the electrical system?